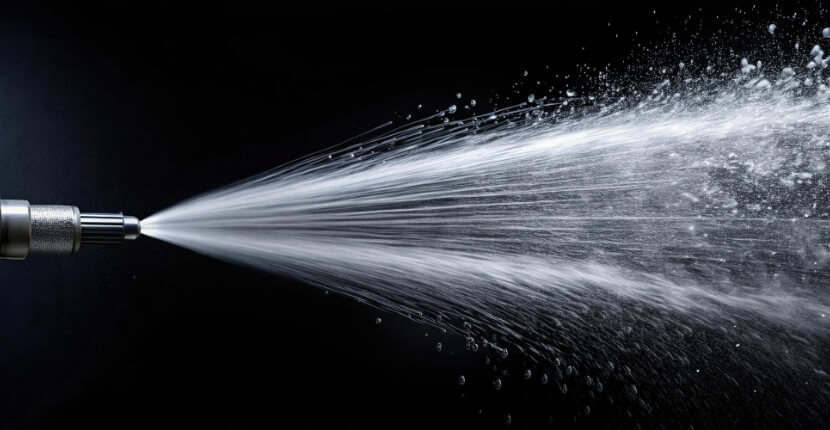
Wet Blasting
Enquire Today For A Free No Obligation Quote
At Wet Blasting, we provide specialist surface cleaning, preparation, and restoration services using wet blasting technology across the UK.
Wet blasting is the process of combining water and abrasive media to remove coatings, rust, or residues while protecting the integrity of the underlying surface.
Since this method generates no heat or dust, it is ideal for delicate materials, precision components, and environments where dry blasting is too aggressive.
Restore your surface the right way — get your free wet blasting quote today.
What Is Wet Blasting?
Wet blasting is a surface treatment process that uses a mix of water and abrasive media to clean, strip, or prepare surfaces without damaging the underlying material.
The technique works by propelling this mixture under pressure, allowing for effective removal of rust, paint, grease, or scale.
As water cushions the abrasive action, wet blasting produces no dust, generates less heat, and offers a more controlled finish than traditional dry blasting.
How Much Does Wet Blasting Cost?
The cost of wet blasting is between £50 and £100 per hour.
The cost depends on the surface type, contamination level, and job complexity.
Flat-rate pricing may be available for specific components, such as alloy wheels or engine parts.
To ensure value and suitability, we assess each project individually and provide a transparent, no-obligation quote.
What Are the Benefits of Wet Blasting?
Wet blasting offers a clean, safe, and controlled way to remove coatings and prepare surfaces without damaging the underlying material.
Key benefits include:
- Dust-free operation that improves air quality and reduces contamination.
- Minimal heat generation, protecting sensitive surfaces and components.
- Even, satin-like finishes that improve coating adhesion.
- Reduced abrasive usage, making the process more environmentally friendly.
- Compatibility with metal, plastic, glass, ceramic, and composite materials.
- No embedded media in the substrate, reducing post-treatment requirements.
- Suitable for both restoration and precision surface preparation.
- Lower risk of surface distortion compared to dry blasting.
- Excellent for delicate or complex geometries with tight tolerances.
- Eliminates the risk of static build-up during blasting.
- Quieter operation compared to dry blasting methods.
- Improved safety in enclosed or cleanroom environments.
- Faster cleanup with less airborne debris and waste.
- Allows for post-blast treatments like coating or painting without surface contamination.
How Does Wet Blasting Work?
Wet blasting works by mixing abrasive particles with water and propelling the slurry through a nozzle under controlled pressure.
The water acts as a lubricant and carrier, softening the impact of the abrasive media on the surface.
Since the process uses a fluid medium, it creates a smoother finish, limits dust, and prevents static build-up.
What Can Wet Blasting Be Used For?
Wet blasting is used for cleaning, degreasing, descaling, surface preparation, and cosmetic finishing.
It is commonly applied in industries such as automotive restoration, aerospace, marine maintenance, manufacturing, engineering, and historic preservation.
As the process is gentle yet effective, it’s ideal for aluminium, stainless steel, titanium, and delicate components that require a clean finish without material loss.
What Is the Difference Between Wet Blasting and Dry Blasting?
Wet blasting uses a mixture of water and abrasive media, while dry blasting uses only abrasive propelled by air.
The addition of water in wet blasting cushions the abrasive action, reducing dust, heat, and surface damage during treatment.
Since wet blasting is more controlled and less aggressive, it is better suited to delicate materials, enclosed spaces, and precision surface preparation.
What Surfaces Can Be Treated With Wet Blasting?
Wet blasting can treat metals, plastics, ceramics, composites, and glass.
It is effective on ferrous and non-ferrous metals, including aluminium, steel, brass, and titanium.
As the process is non-destructive, it is suitable for both hard and soft materials without causing warping or surface damage.
Can Wet Blasting Remove Paint and Rust?
Wet blasting effectively removes paint, rust, and corrosion from a wide range of surfaces without damaging the base material.
The abrasive-water mix gently strips away coatings while maintaining the integrity of metals, plastics, and composites.
Since the process avoids high heat and aggressive abrasion, it is ideal for restoring surfaces where dry blasting would be too harsh or leave pitting.
Is Wet Blasting Suitable for Alloy Wheels?
Wet blasting is an ideal method for cleaning and refurbishing alloy wheels.
It removes brake dust, corrosion, and old coatings while maintaining the shape and finish of the wheel.
As alloy surfaces are easily damaged by harsh media or heat, the wet blasting process provides a safer, more controlled finish.
What’s the Best Media to Use in Wet Blasting?
The best media for wet blasting depends on the surface material and the finish required.
Common options include glass bead for fine cosmetic finishes, aluminium oxide for aggressive cleaning, and plastic media for softer surfaces.
Since different applications require different levels of abrasion, the correct media is selected based on the part’s condition and sensitivity.
Does Wet Blasting Require Post-Treatment?
Most wet blasted surfaces require some form of post-treatment such as rinsing, drying, or coating application.
Although wet blasting leaves a clean, smooth finish, unprotected metal may flash rust if left exposed.
As the surface is ideal for adhesion, applying a primer, protective sealant, or final coating immediately helps preserve the result.
Is Wet Blasting Safe for Delicate or Precision Parts?
Wet blasting is highly suitable for delicate and precision-engineered parts due to its low-impact application.
The water-based process prevents heat build-up and cushions abrasive force, which helps preserve dimensional accuracy.
Since many precision components require surface preparation without material removal, wet blasting offers a safe, consistent solution.
Is Wet Blasting Environmentally Friendly?
Wet blasting is considered more environmentally friendly than dry blasting due to its lower dust output and reduced abrasive consumption.
The closed-loop systems used in many wet blasting units allow for water and media recycling, which reduces waste and improves sustainability.
As there is less airborne contamination, it also supports safer working environments and easier compliance with environmental regulations.
How Long Does Wet Blasting Take?
Wet blasting takes between 15 minutes and 2 hours.
The duration of wet blasting depends on the part size, surface condition, and level of contamination.
Smaller items such as brackets or engine parts may be completed in under 30 minutes, while larger or heavily corroded components may require more time.
Since each job has unique requirements, we assess every part to ensure the process is both thorough and time-efficient.
Can Wet Blasting Be Done On-Site?
Wet blasting can be performed both at our dedicated facility and on-site, depending on access and the nature of the job.
Mobile wet blasting units are available for larger structures or immovable components that require in-situ cleaning or preparation.
As containment and drainage must be managed properly, site assessments are carried out before any mobile work is scheduled.
How Should Surfaces Be Maintained After Wet Blasting?
After wet blasting, surfaces should be rinsed, dried, and protected to prevent flash rust or contamination.
Metal surfaces may require the application of a corrosion inhibitor, primer, or protective coating shortly after treatment.
Since wet blasting cleans to a reactive finish, immediate follow-up treatments help preserve the cleaned surface.
Can Wet Blasting Be Used Before Painting or Coating?
Wet blasting is an ideal surface preparation method before painting, powder coating, or anodising.
It removes dirt, grease, corrosion, and previous coatings while producing a smooth, etched surface that promotes strong adhesion.
As the process leaves no embedded media or residue, treated parts are immediately ready for coating when properly dried.
Is Wet Blasting Suitable for Engine Parts?
Wet blasting is widely used for cleaning engine parts such as cylinder heads, intake manifolds, crankcases, and carburettors.
It effectively removes carbon deposits, oil residue, and corrosion without damaging machined surfaces or internal structures.
Since precision and cleanliness are critical in engine refurbishment, wet blasting offers a reliable and non-destructive solution.
How Can I Get a Free Wet Blasting Quote?
Get a wet blasting quote by completing our online request form to share your project details.
We’ll ask a few quick questions about your surface type, contamination level, and desired outcome before issuing a detailed quotation.
Whether it’s a one-off item or ongoing contract work, we’ll make sure your quote reflects your timeline and technical needs.
Tell us what you need — and we’ll get the quote to you fast.
Find More Info
Make sure you contact us today for a number of great Wet Blasting services.
For more information on Wet Blasting, fill in the contact form below to receive a free quote today.
★★★★★
First-rate job and cracking customer service. Wet Blasting handled our alloy wheels better than expected – smooth, clean, and no damage whatsoever. Will be recommending to others without hesitation.
Callum Dorrington
Greater London
★★★★★
Absolutely brilliant service from start to finish. Wet Blasting restored our vintage motorbike parts to like-new condition with real attention to detail. You can tell they take pride in their craft. Hats off to the team!
Imogen Featherstone
Greater London